PSA Oxygen Unit
Ambient air mainly consists of 78% nitrogen, 21% oxygen, 0.9% argon, and 0.1% other gases. Meanwhile HAVAYAR industrial group has been focused on producing oxygen as one of the most vital industrial gases which is widely used in hospitals and medical facilities. In this regard, there are two general methods to produce oxygen. The first method is cryogenic plant which produces liquid oxygen with a very high level of purity.
Ambient air mainly consists of 78% nitrogen, 21% oxygen, 0.9% argon, and 0.1% other gases. Meanwhile HAVAYAR industrial group has been focused on producing oxygen as one of the most vital industrial gases which is widely used in hospitals and medical facilities. In this regard, there are two general methods to produce oxygen. The first method is cryogenic plant which produces liquid oxygen with a very high level of purity.
Ambient air mainly consists of 78% nitrogen, 21% oxygen, 0.9% argon, and 0.1% other gases. Meanwhile HAVAYAR industrial group has been focused on producing oxygen as one of the most vital industrial gases which is widely used in hospitals and medical facilities. In this regard, there are two general methods to produce oxygen. The first method is cryogenic plant which produces liquid oxygen with a very high level of purity. Pressure swing absorption (PSA), which is a feasible technology to produce oxygen in the vicinity of demand zone, is the second technique. In PSA oxygen production systems which work with the principle of physical adsorption, compressed air passes through a special adsorbent material called zeolite which causes the separation of other components of air like nitrogen and finally pure oxygen with an approximate concentration of 90-95% leaves the tower. In this technology, air components are separated by the porous absorbent surface and once the adsorbent molecules reaches the saturated state, the regeneration process starts by reducing the pressure. It should be mentioned that in PSA type oxygen generators, there are two columns fulfilled with zeolite. One column produces oxygen and the other one releases absorbed nitrogen. In other words, at the same time as the first column is in the adsorption mode, the other one is in regeneration mode. The procedure of regeneration starts with sudden discharge and subsequently passage of pure oxygen in the column with the aim of nitrogen removal from adsorbent material. Within a predetermined period of time, the roles of adsorption and regeneration columns change. This is illustrated in the figure below.
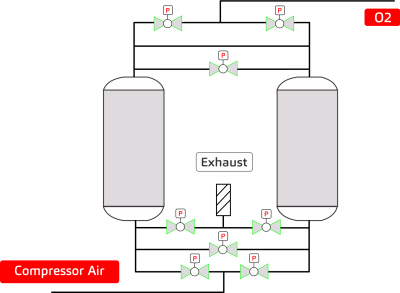
HAVAYAR Industrial Group has the ability of engineering, supplying, installing, commissioning and overhauling oxygen production packages with different capacities and purities. Today HAVAYAR Oxygen generator can produce oxygen with mass flow rate and purity of up to 96 Nm3/hr and 95% respectively. As these values differ for various oxygen generator models of this company, device model is determined and selected according to the customer’s needs. It also should be mentioned that in the PSA oxygen generator, the inlet air pressure is around 5 to 7 bar gauge and the output pressure of the device is between 4 to 6 bar gauge.
It should be noted that the processes followed in an integrated PSA packages can be listed as follows:
- Compression of atmospheric air in the compressor.
- Separation of moisture in the air by absorption or refrigeration dryer.
- Filtration includes three series of filters with a filtration degree of 1 μm, 0.01 μm and a final antibacterial filter (absorbing bacteria up to 0.0001%), in each of which the output fluid flow is filtered in different sizes.
- Oxygen production in the oxygen generator.
- Air and oxygen receiving (one for receiving the air flow coming out of the compressor and another for receiving oxygen)
Also, an oxygen generation package consists of the following key components:
- Cylindrical pressure vessels fulfilled with adsorbent.
- Adsorbent material (zeolite)
- Sensors, pressure gauges, and oxygen analyzer.
- Flow control valves
- Control panel
In the field of designing and producing oxygen packages, the following actions are carried out in HAVAYAR Industrial Group:
- Detailed engineering and design of the package based on the customer’s needs.
- Coordination and selection of suppliers based on customer request.
- Inspection and testing of equipment and consumable parts.
- Production of all technical documents required for the project.
- Holding design, layout, construction, operation and maintenance review meetings.
- Pre commissioning, commissioning and operators training.
The benefits of using HAVAYAR oxygen generator
- Taking advantage of the most modern oxygen generators based on the state of the art technology.
- Using the best and highest quality zeolites.
- 100% automatic operation without the need for an operator.
- Having a PLC with the ability to display the percentage of purity, pressure and capacity of the produced oxygen and display the complete pressure trend on the touch screen.
- Having a zirconium oxide type oxygen analyzer with a long life time (no need to replace).
- Minimum energy requirement due to the lower air consumption compared to the similar devices.
- The possibility of adjusting the degree to prevent the exit of oxygen with a purity lower than the value determined by the cut off system.
- Minimal noise pollution.
- Ease of maintenance, repair and service.
Frequently Asked Questions
There are two general methods to produce oxygen. The first method is cryogenic plant which produces liquid oxygen with a very high level of purity. Pressure swing absorption (PSA), which is a feasible technology to produce oxygen in the vicinity of demand zone, is the second technique.
In PSA oxygen production systems which work with the principle of physical adsorption, compressed air passes through a special adsorbent material called zeolite which causes the separation of other components of air like nitrogen and finally pure oxygen with an approximate concentration of 90-95% leaves the tower. In this technology, air components are separated by the porous absorbent surface and once the adsorbent molecules reaches the saturated state, the regeneration process starts by reducing the pressure. It should be mentioned that in PSA type oxygen generators, there are two columns fulfilled with zeolite. One column produces oxygen and the other one releases absorbed nitrogen. In other words, at the same time as the first column is in the adsorption mode, the other one is in regeneration mode. The procedure of regeneration starts with sudden discharge and subsequently passage of pure oxygen in the column with the aim of nitrogen removal from adsorbent material. Within a predetermined period of time, the roles of adsorption and regeneration columns change.
1. Taking advantage of the most modern oxygen generators based on the state of the art technology. 2. Using the best and highest quality zeolites. 3. 100% automatic operation without the need for an operator. 4. Having a PLC with the ability to display the percentage of purity, pressure and capacity of the produced oxygen and display the complete pressure trend on the touch screen. 5. Having a zirconium oxide type oxygen analyzer with a long life time (no need to replace). 6. Minimum energy requirement due to the lower air consumption compared to the similar devices. 7. The possibility of adjusting the degree to prevent the exit of oxygen with a purity lower than the value determined by the cut off system. 8. Minimal noise pollution. 9. Ease of maintenance, repair and service.
sales department
after sales service
datasheet
catalogue