Oxygen is considered as a key biotic compound that the presence of it is vital for continuation of life of living organisms. Due to the air pollution, the oxygen content of atmospheric air may not be beneficial for the group of people with physical problems like lung and respiratory diseases. In this way, atmospheric air usage may aggravate health problems. One of the devices intended for respiratory patients is an oxygen generator.
The oxygen generator has a structure which can adsorb and accumulate the oxygen content the air and thus provide the patient with healthy and high-purity oxygen. The working principle of this equipment is in such a way that it can separate the nitrogen in the air and delivers high purity oxygen (about 93% ± 2) to the patient.
Before invention of Oxygen generators, special capsules were used to provide pure oxygen to the patient. While the technology of producing oxygen through the method of Pressure Swing Adsorption (PSA) is a way of producing continuous oxygen at the point of consumption.
Production by pressure swing adsorption (PSA)
Ambient air mainly consists of 78% nitrogen, 21% oxygen, 0.9% argon, and 0.1% other gases. Therefore, by employing adsorption methods, undesirable compounds can be separated from the air which results in increasing the concentration of desirable elements in the output flow. For low to medium capacity oxygen generators, HAVAYAR industrial group employs Pressure Swing Adsorption or PSA technology in its products, which is a method of producing continuous flow of oxygen at the consumer’s place.
The philosophy of Oxygen production through PSA technology is based on the passage of compressed air through artificial zeolite granules, which are so called molecular sieves. The nitrogen in the air is trapped while passing through the zeolite, and the oxygen in the air leaves the adsorption column at low pressure (about 4 to 6 bar gauge). This generally leads to continuous oxygen production.
The phenomenon of separating oxygen from air components is a physical process where no chemical interaction. As soon as depressurization occurs, the nitrogen gas is eliminated from zeolite granules (known as adsorber material) and discharged which causes the zeolite returns to its original state. In other words, zeolite is regenerated.
The produced oxygen flow rate in the oxygen generators manufactured by HAVAYAR is up to more than 1000 liters per minute in special models and the purity ranges between 91% and 95%. As each model has its own oxygen flow range, the selected model is determined according to the customer’s needs. It also should be mentioned that in oxygen generators, the inlet air pressure is around 5 to 7 barg and the outlet stream pressure ranges between 4 and 6 barg.
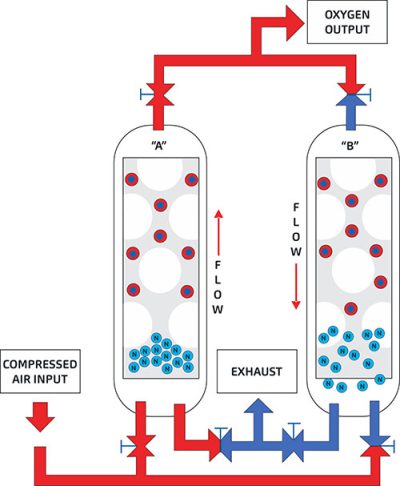
Advantages of oxygen production by PSA method
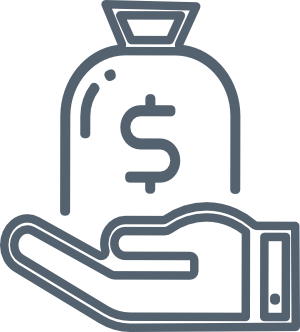
Cost (you have full control over the cost):
Regardless of the capital costs for the purchase of an oxygen generator, producing each cubic meter of oxygen with a purity of 93% by the PSA method, compared to providing the same amount of oxygen using traditional systems such as storage cylinders, reduces operational costs during oxygen production by 80%. In this method, electricity expenditures has the most share in operational costs.
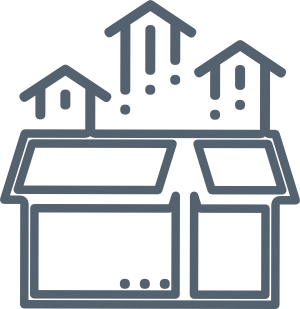
Production at the consumer's place:
PSA oxygen generators have the ability to produce oxygen with the required flow rate at the consumer’s site without imposing slag costs such as the cost of purchasing oxygen capsules continuously. In this method, oxygen will be available, whenever you need by turning the system on.
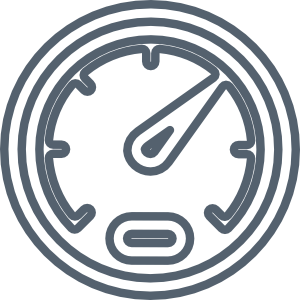
Oxygen pressure
By directing the produced oxygen towards the oxygen receiver tank, it is possible to guarantee the continuous supply and production of oxygen at a pressure between 4 and 6 barg.
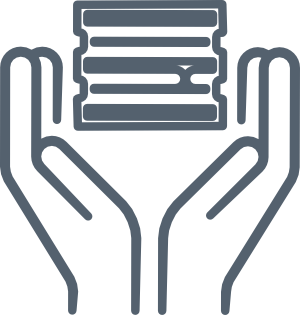
Accessibility
With this method of oxygen production (PSA), the required amount of oxygen can be produced at any time of the day/year.
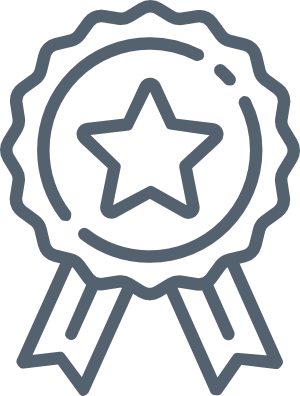
Oxygen quality
PSA oxygen generators are capable to produce high quality oxygen based on the requirements of Iran’s national standard 10766. It is worth noting that the requirements of this standard are mandatory according to the executive instructions of the General Department of Medical Equipment of the Ministry of Health, Treatment and Medical Education for medical oxygen generators using the PSA method.
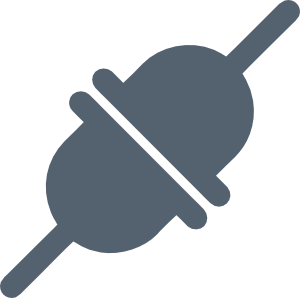
Connection to the hospital pipeline
The mentioned oxygen generation system can be directly connected to the hospital’s oxygen distribution pipeline. Also, by using oxygen storage tanks in conjunction with the oxygen production system, in case of a pressure or purity drop for any reason, including a power cut, the storage system will immediately enter the circuit and there will be no interruption in oxygen supply.
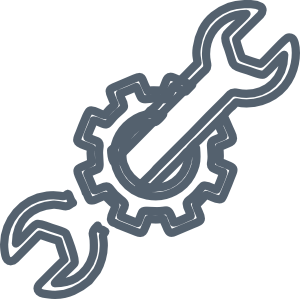
Easy maintenance
Usually only once every 3 months, the filter elements of HAVAYAR’s oxygen generators need to be replaced. Also this type of oxygen generators requires service and maintenance to be done by HAVAYAR’s authorized service experts.
Advanced filtration:
By using multi-stage filtration at the inlet of the oxygen generator and preventing the entry of any impurities (including oil, water, dust, etc.) into the oxygen generator, the life time of the zeolite material will be enhanced and the quality of outlet oxygen will be guaranteed. With antibacterial filters and a fine filter stage, the outgoing oxygen will be free from any harmful particles for the patient.
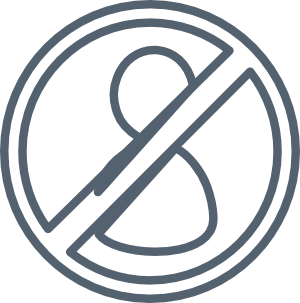
100% automatic operation without the need for an operator
PSA oxygen generator components
Device structure:
- Equipped with epoxy paint coating and resistant to corrosive environments
- using copper or stainless-steel fittings in piping
- Optimum design in space occupation which results in minimum required space
- passing all quality control tests during construction
- Design based on standards approved by the General Department of Medical Equipment
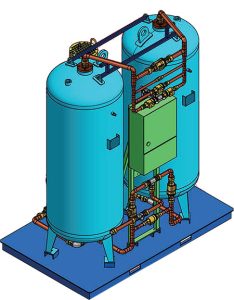
Valves
- High Quality
- High safety
- Special design
- using reputable brands
- Valid certificates
- Long life and low failure
- High performance capability in high duty cycles
- containing an actuator (up to 60% saving in valve space)
ZEOLITE adsorbent material (13X Molecular Sieve)
- High efficiency
- Long life time
- Appropriate mechanical strength
- Suitable for use in industries and medical equipment
Oxygen sensor
- Long life
- Functional range from 0 to 96%
- High accuracy of 0.01%
- passed valid European standards
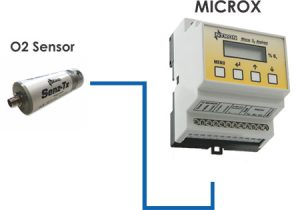
Silencer
- Noise reduction to less than 85db
- passing valid European standards
- Proper appearance and preventing the device from propagating high-level noise during operation
In order to control the operation of the oxygen generator, PLC model S7-1200 manufactured by Siemens is used along with a 7-inch touch screen, the most important features of this type of PLC can be listed as follows:
- IP54 degree of protection
- Ability to connect to Ethernet.
- The ability to set the operational time sequence of each of the control valves on the device.
- The ability to display and observe the purity and pressure of the product permanently and continuously.
- The ability to view the list of device alarms and saving these alarms on the device storage.
- The ability to view the device’s operating time and detect when the device’s service time is reached.
- Ability to send Common Alarm and Running Status signals to the client’s central control panel.
- Displaying the operation status of the device and the open and closed state of the control valves.
- depicting variation of purity and pressure with changes in time to observe possible fluctuations and ensure the performance of each component of the device
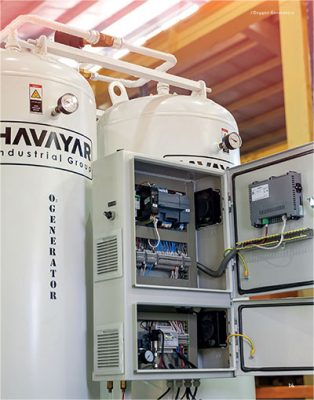
Oxygen production capacity (Slit/min) | model |
12.3 | 0-10 |
27.3 | 0-20 |
38.7 | 0-40 |
52.9 | 0-60 |
82 | 0-70 |
130 | 0-100 |
193 | 0-170 |
271 | 0-230 |
399 | 0-330 |
600 | 0-500 |
792 | 0-600 |
1186 | 0-800 |
1584 | O-600×2 |
Oxygen production capacity (Slit/min) | model |
12.3 | 0-10 |
27.3 | 0-20 |
38.7 | 0-40 |
52.9 | 0-60 |
82 | 0-70 |
130 | 0-100 |
193 | 0-170 |
271 | 0-230 |
399 | 0-330 |
600 | 0-500 |
792 | 0-600 |
1186 | 0-800 |
1584 | 0-600×2 |
- The announced capacity is related to the purity of 93 ± 2%.
- Pressure ranges between 4 and 6 bar.
How to choose a medical oxygen generator
The governing factors of an oxygen generator selection can be listed as follows:
- The selection of the oxygen generator is performed by determination of the required oxygen flow rate by the client (hospital)
- Recommendations for size and capacity according to Iran’s national standard
Hospital required oxygen capacity determination:
Choosing a proper oxygen generation device based on the calculated required oxygen capacity includes the following steps:
- Sizing and selection of the compressor suitable for the oxygen generator device.
- Sizing and selection of dryer suitable for compressor and oxygen generator.
- Sizing and selection of filtration system suitable for compressor, oxygen generator and dryer.
- Sizing and selection of air storage tanks according to the selected components.
- Sizing and selection of oxygen receivers according to hospital consumption and production of oxygen generator and the time required to cover the specified demand.
Medical oxygen generator arrangement
- Air compressor
- Water Separator
- Dryer
- Filtration (oil trap, water trap, dust)
- Air buffer tank (Air Buffer Receiver)
- PSA oxygen generator (O2 Generator)
- Oxygen tank (Oxygen Receiver)
- Anti-bacterial filter
- Connections and piping
- Purity and output flow display system
- Connecting manifold of oxygen generator system and capsule backup system